自社に3Dプリンターを導入。問題解決提案が出来ます。
押出・コンプレッション・インジェクション成形による量産まで
一貫した製品のご提案が可能です。
弊社ではポリマー・ソリューション・エキスパートとして3Dプリンターを用いた試作のご提案から、
押出成形、コンプレッション成形、インジェクション成形による量産までのご対応を行っております。
ここではほんの一例ですがその事例をご案内させて頂きます。
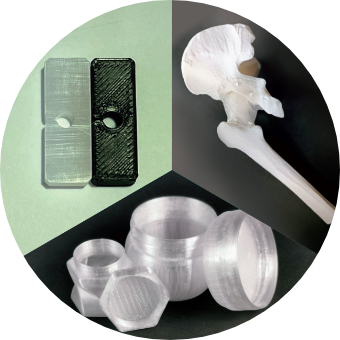
事例-1 量産費用の削減例
靱帯手術練習用モデルの検討案件を頂きました。
従来の輸入品モデルは練習使用後全て廃棄をしており、それをコストダウン出来ないかとのご案件でした。
弊社にて靱帯部分(透明部分 シリコーンゴム製)を脱着式仕様にする事と、3Dプリンターを用いて全てを製作する事を提案させて頂いた事で約50%という大幅なコストダウンを実現しました。
また、サイズも従来品よりコンパクトとなった為持ち運びが容易となり、お客様の全営業へ配布される事になりました。
材質:PLA+シリコーンゴム
効果:従来品からのコスト低減:約50%
ワンウェイでの使用から脱着式による
廃棄の削減(環境貢献)
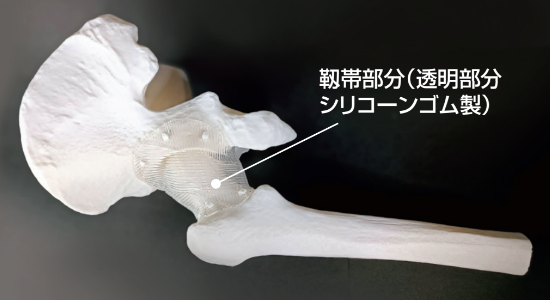
事例-2 試作量産費用の削減例(コンプレッション成形)
機械系商社様より、家電用部品のご相談を頂きました。
ゴムグロメットのご相談でしたが、開発案件が至急という事もあり金型を製作する前にHPフィラメント(スーパーフレキシブルタイプ)を用い、充填率による硬度調整を実施し3Dプリンターで1mm違いの製品を3サイズ作成し実際に組込んで確認を行って頂きました。
3点の中で最も篏合が良いサイズを選定頂き、その後海外の協力工場にてコンプレッション成型金型を製作し、試作納期の短縮と修正費用の削減、及び量産費用の削減を行うことが出来ました。
材質:3D造形⇒HPフィラメント(スーパーフレキシブルタイプ)
充填率50%(JISA 50°想定)
量産⇒シリコーンゴム50°(JISA)
効果:試作金型製作せずに試作金型製作のコスト削減
3D試作造形スケジュール1日で開発時間短縮
海外メーカーへの発注による量産コストの削減
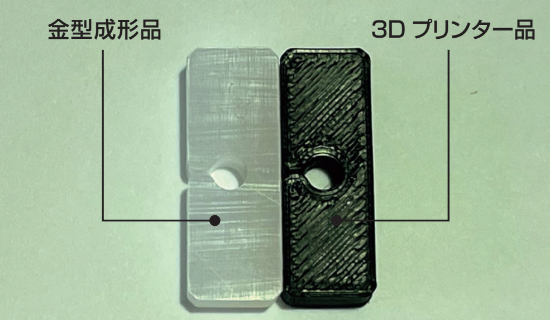
事例-3 試作費用の削減例(押出成形)
ドア部品のコーナーカバーとしてご案件を頂きました。
従来であれば、押出金型作成の上テストしその具合により修正、または金型再作となっていました。
押出金型を作成する前に3Dプリンターにて試作品を作成し評価する事で、トライアンドエラーによる費用の削減となりました。
材質:PVC
初期投資額(押出金型費):¥650,000-
3Dプリンターで試作作成
材質:ポリ乳酸(PLA)
試作費用:¥10,000-
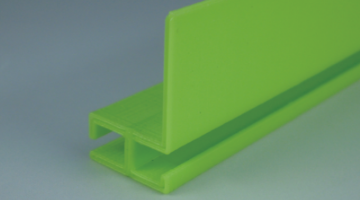
3m位の長尺造形も可能です。
事例-4 試作費用の削減例(押出成形)
浴室部品のセットアップ材としてのご案件を頂きました。
弊社にて押出成形がし易い形状をご提案させて頂き、硬質部分を作成し弊社ゲルを貼り付け「ゲルガスケット」としその具合をご確認頂いた後起型する事をご提案しご採用を頂きました。
材質:PP+HOTTYゲル(ゲルガスケット)
初期投資額(押出金型費):¥450,000-
3Dプリンターで硬質部作成し、ゲルを貼り付け
材質:ポリ乳酸(PLA)+HOTTYゲル
試作費用:¥75,000-
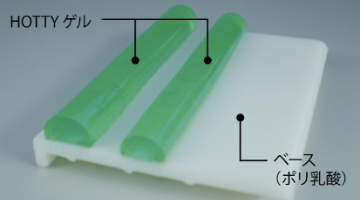
事例-5 試作費用の削減例(押出成形)
浴室部品の止水材としてのご案件を頂きました。
弊社にて押出成形がし易い形状をご提案させて頂き、ポリ乳酸(PLA)で型枠を作成し常温硬化型シリコーンを注入。全長150mm程度の押出サンプルを作成しコーナーの追従性のご提案をさせて頂きました。
材質:EPDMスポンジ
初期投資額(押出金型費):¥60,000-
3Dプリンターで型枠を作成し、常温硬化型シリコーンを成形
材質:ポリ乳酸(PLA)+シリコーンゴム
試作費用:¥10,000-
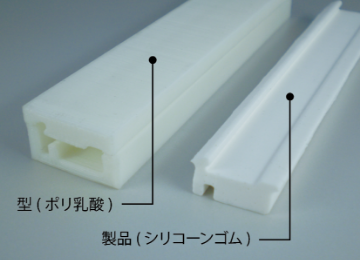
事例-6 量産費用の削減例(コンプレッション成形)
ビル用部品の気密ピースとしてのご案件を頂きました。
ロットが少量であり、金型投資に対しての償却が困難であったため、ポリ乳酸(PLA)で簡易的に型を作成し、常温硬化型シリコーンゴムを充填し硬化させる方法でご提案を行いました。
材質:シリコーンゴム
初期投資額(プレス金型費):¥150,000-
製品代:¥1,000-(ロット5個)
3Dプリンターで型枠を作成し、常温硬化型シリコーンを成形
材質:型⇒ポリ乳酸(PLA)、製品⇒シリコーンゴム
製作費用:型⇒¥15,000-、製品⇒¥1,000-(ロット5個)

ゴム・樹脂のことならお任せください!
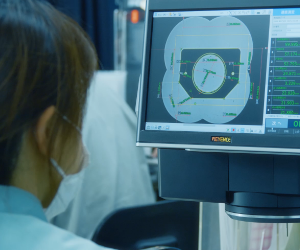
長年に渡る研究・製造の中で、高機能ゴム押出製品や高機能樹脂押出製品では、建材や自動車関連など幅広い分野で高い品質と高い信頼性からご評価いただいております。
長年培った豊富な経験と実績から、ホッティーポリマーだからこそできる、お客様のニーズにあわせた最適なご提案をさせていだきます。